Piston ring
A piston ring is a metallic split ring that is attached to the outer diameter of a piston in an internal combustion engine or steam engine.
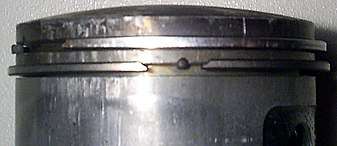
The main functions of piston rings in engines are:
- Sealing the combustion chamber so that there is minimal loss of gases to the crank case.
- Improving heat transfer from the piston to the cylinder wall.
- Maintaining the proper quantity of the oil between the piston and the cylinder wall
- Regulating engine oil consumption by scraping oil from the cylinder walls back to the sump.[1]
Design

A) Rectangular section
B) Barrel face
C) keystone
D) Torsional twist
E) Taper face
F) Dykes
Which also differ for the type of retainer band:
Y) Behind-band
X) Above or under-band
Or for the ends that work without firm stops:
K) Step
J) Oblique
W) Oblique with step

Piston rings are designed to seal the gap between the piston and the cylinder wall.[2] If this gap were too small, thermal expansion of the piston could mean the piston seizes in the cylinder, causing serious damage to the engine. On the other hand, a large gap would cause insufficient sealing of the piston rings against the cylinder walls, resulting in excessive blow-by (combustion gases entering the crankcase) and less pressure on the cylinder, reducing the power output of the engine.
The sliding motion of the piston ring inside the cylinder wall causes friction losses for the engine. The friction caused by piston rings is approximately 24% of the total mechanical friction losses for the engine.[3][4] The design of the piston rings is therefore a compromise between minimising friction while achieving good sealing and an acceptable lifespan.
Lubrication of piston rings is difficult and has been a driving force to improvements in the quality of motor oil. The oil must survive high temperatures and harsh conditions with a high-speed sliding contact. Lubrication is particularly difficult as the rings have an oscillating motion rather than continuous rotation (such as in a bearing journal). At the limits of piston movement, the ring stops and reverses direction. This disrupts the normal oil wedge effect of a hydrodynamic bearing, reducing the effectiveness of the lubrication.
Rings are also sprung to increase the contact force and to maintain a close seal. The spring force is provided by either the stiffness of the ring itself or by a separate spring behind the seal ring.
It is important that rings float freely in their grooves within the piston, so that they can stay in contact with the cylinder.[5] Rings binding in the piston, usually due to a build-up of either combustion products or a breakdown of the lubricating oil, can cause engine failure and is a common cause of failure for diesel engines.
Number of rings
Sealing is often achieved by multiple rings, each with their own function, using a metal-on-metal sliding contact. Most pistons have at least two piston rings per cylinder.
Automotive piston engines typically have three rings per cylinder.[6] The top two rings— known as compression rings— are primarily for sealing the combustion chamber. The bottom ring— known as the oil control ring— is primarily for controlling the supply of oil to the cylinder wall, in order to lubricate the piston skirt and the oil control rings.[7]
Ring construction
The compression rings in an automotive engine typically have a rectangular or keystone shaped cross-section. The upper compression ring typically has a barrell profile for the periphery, while the lower compression ring typically has a taper napier facing. Some engines also use a taper facing for the top ring, and simple plain-faced rings were used in the past.
Oil control rings are typically made from either a single piece of cast iron, multiple pieces of steel, or steel/iron with a helical spring backing to create the tension required for a close seal. Cast iron oil rings and rings with a helical spring backing have two scraping lands of various detailed form. On the other hand, multi-piece steel oil control rings usually consist of two thin steel rings (called rails) with a spacer-expander spring between them to keep the two rails apart and provide radial pressure.
The gap in the piston ring compresses to a few thousandths of an inch when inside the cylinder bore. Ring gap shapes include square cut, angle cut, tite joint, step cut, hook step and mitre step.[8]
History
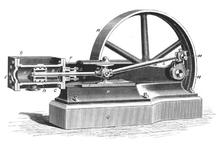
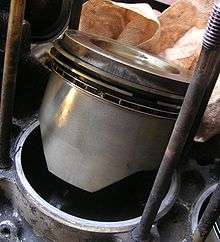
Early steam engines used a hemp packing to seal the combustion chamber,[9] which caused high frictional resistance and did not provide a very effective seal.
The modern design of a metallic split-ring was invented by John Ramsbottom in the 1850s. Ramsbottom's initial design in 1852 was a circular shape, however these wore unevenly and were not successful. In 1854, a revised design was claimed to have a lifespan of up to 4,000 mi (6,437 km).[10] This was based on the discovery that a perfectly round (prior to installation) ring with a split in it does not exert an even pressure on the cylinder walls once installed. The revised piston ring was manufactured to an out-of-round shape, so that it would exert even pressure once installed in the cylinder. An 1855 patent documented this change. The switch to metallic piston rings dramatically reduced the frictional resistance, the leakage of steam, and the mass of the piston, leading to significant increases in power and efficiency and longer maintenance intervals.
Engine wear
Piston rings are subject to wear as they move up and down the cylinder bore, due to their own inherent load and due to the gas load acting on the ring. To minimize this, they are made of wear-resistant materials, such as cast iron and steel, and are coated or treated to enhance the wear resistance. Coatings used in modern motorcycles include chromium,[11] nitride,[12] or ceramic coating made by plasma deposition[13] or physical vapour deposition (PVD).[14][15] Most modern diesel engines have top rings coated with a modified chromium coating (known as CKS or GDC),[11] which has aluminium oxide or diamond particles respectively included in the chrome surface.
In two-stroke engines, the port design is also an important factor for the lifespan of the piston rings.
See also
References
- "General Principles". www.federalmogul.com. Retrieved 1 December 2019.
- "Piston Ring Functions and Operation". www.federalmogul.com. Archived from the original on 10 July 2011. Retrieved 1 July 2009.
- "VCI 2840 - Carbon films - Basic knowledge, film types and properties". VDI-Fachbereich Produktionstechnik und Fertigungsverfahren (in German) (June 2012). Retrieved 1 December 2019.
- "Piston Ring Coating Reduces Gasoline Engine Friction" (PDF). www.federalmogul.com. Archived from the original (PDF) on 24 September 2015.
- "Piston Rings". www.globmaritime.com. Archived from the original on 2 June 2014.
- "Factors influencing oil control in a spark ignited gasoline engine". www.hastingsmfg.com. Archived from the original on 31 March 2008.
- "Piston & Piston Ring Assembly". www.riken.co.jp. Archived from the original on 19 August 2002.
- "Custom Ring Gaps". www.precisionrings.com. Archived from the original on 6 July 2017.
- Weiss, Alex (2008). Bearings (Workshop Practice). Special Interest Model. ISBN 978-1854862501.
- "Proceedings Institution of Mechanical Engineers to 1859". www.steamindex.com. Retrieved 4 December 2019.
- "Wear-Resistant Peripheral Coatings". www.federalmogul.com. Archived from the original on 14 July 2012. Retrieved 4 July 2010.
- "Wear-Resistant Peripheral Coatings". www.federalmogul.com. Archived from the original on 14 July 2012. Retrieved 4 July 2010.
- "Wear-Resistant Peripheral Coatings". www.federalmogul.com. Archived from the original on 14 July 2012. Retrieved 4 July 2010.
- "Wear-Resistant Peripheral Coatings". www.federalmogul.com. Archived from the original on 14 July 2012. Retrieved 4 July 2010.
- "Metallic piston rings product sheet" (PDF). www.grovercorp.com. Archived from the original (PDF) on 6 July 2016. Retrieved 8 December 2019.
![]() |
Wikimedia Commons has media related to Piston rings. |