Robotic arm
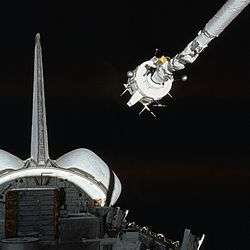
A robotic arm is a type of mechanical arm, usually programmable, with similar functions to a human arm; the arm may be the sum total of the mechanism or may be part of a more complex robot. The links of such a manipulator are connected by joints allowing either rotational motion (such as in an articulated robot) or translational (linear) displacement.[1][2] The links of the manipulator can be considered to form a kinematic chain. The terminus of the kinematic chain of the manipulator is called the end effector and it is analogous to the human hand.
Robotic hand


The end effector, or robotic hand, can be designed to perform any desired task such as welding, gripping, spinning etc., depending on the application. For example, robot arms in automotive assembly lines perform a variety of tasks such as welding and parts rotation and placement during assembly. In some circumstances, close emulation of the human hand is desired, as in robots designed to conduct bomb disarmament and disposal.[5]
Types
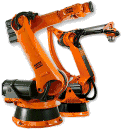
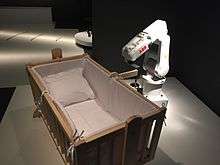
- Cartesian robot / Gantry robot: Used for pick and place work, application of sealant, assembly operations, handling machine tools and arc welding. It's a robot whose arm has three prismatic joints, whose axes are coincident with a Cartesian coordinator.
- Cylindrical robot: Used for assembly operations, handling at machine tools, spot welding, and handling at diecasting machines. It's a robot whose axes form a cylindrical coordinate system.
- Spherical robot / Polar robot Used for handling machine tools, spot welding, diecasting, fettling machines, gas welding and arc welding. It's a robot whose axes form a polar coordinate system.
- SCARA robot: Used for pick and place work, application of sealant, assembly operations and handling machine tools. This robot features two parallel rotary joints to provide compliance in a plane.
- Articulated robot: Used for assembly operations, diecasting, fettling machines, gas welding, arc welding and spray painting. It's a robot whose arm has at least three rotary joints.
- Parallel robot: One use is a mobile platform handling cockpit flight simulators. It's a robot whose arms have concurrent prismatic or rotary joints.
- Anthropomorphic robot: It is shaped in a way that resembles a human hand, i.e. with independent fingers and thumbs.
Notable robotic arms
.jpg)
In space, the Space Shuttle Remote Manipulator System also known as Canadarm or SRMS and its successor Canadarm2 are examples of multi degree of freedom robotic arms. These robotic arms have been used to perform a variety of tasks such as inspection of the Space Shuttle using a specially deployed boom with cameras and sensors attached at the end effector, and also satellite deployment and retrieval manoeuvres from the cargo bay of the Space Shuttle.[6]
The Curiosity rover on the planet Mars also uses a robotic arm.[7][8][9][10]
Low-cost robotic arms
In the decade of 2010 the availability of low-cost robotic arms increased substantially. Although such robotic arms are mostly marketed as hobby or educational devices, applications in laboratory automation have been proposed, like their use as autosamplers.[11][12]
See also
References
- ↑ OSHA Technical Manual
- ↑ Paper on Space Robotics, pg 9
- ↑ "Robot Arm and Computer Vision". Retrieved 29 July 2016.
- ↑ "MeArm Open Source Robot Arm (source files)". Retrieved 21 June 2016.
- ↑ Staff (Sandia National Labs) (August 16, 2012), "Life-like, cost-effective robotic hand can disable IEDs", R&D Magazine, rdmag.com, retrieved September 13, 2012
- ↑ IEEE Xplore:The Canadarm grasps this boom and can position it in the necessary positions to permit a complete inspection
- ↑ "Curiosity Rover - Arm and Hand". JPL. NASA. Retrieved 2012-08-21.
- ↑ Jandura, Louise. "Mars Science Laboratory Sample Acquisition, Sample Processing and Handling: Subsystem Design and Test Challenges" (PDF). JPL. NASA. Retrieved 2012-08-21.
- ↑ "Curiosity Stretches its Arm". JPL. NASA. 21 August 2012. Retrieved 2012-08-21.
- ↑ Billing, Rius; Fleischner, Richard (2011). "Mars Science Laboratory Robotic Arm" (PDF). 15th European Space Mechanisms and Tribology Symposium 2011. Retrieved 2012-08-21.
- ↑ Carvalho, Matheus C.; Eyre, Bradley D. (2013-12-01). "A low cost, easy to build, portable, and universal autosampler for liquids". Methods in Oceanography. 8: 23–32. doi:10.1016/j.mio.2014.06.001.
- ↑ McMorran, Darren; Chung, Dwayne Chung Kim; Li, Jonathan; Muradoglu, Murat; Liew, Oi Wah; Ng, Tuck Wah (2016-02-16). "Adapting a Low-Cost Selective Compliant Articulated Robotic Arm for Spillage Avoidance". Journal of Laboratory Automation: 2211068216630742. doi:10.1177/2211068216630742. ISSN 2211-0682. PMID 26882923.