Filterpers
Een filterpers of filterkamerpers is een toestel om vaste stof en vloeistof te scheiden. Het werd in de 19e eeuw ontwikkeld om klei te ontwateren[1]. Processen in de voedingsindustrie, chemische industrie, farmaceutische industrie maken producten uit een suspensie van vaste stof in een vloeistof.
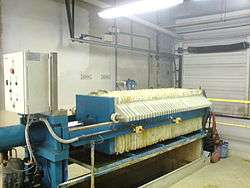
Een filterpers bestaat uit vierkante, rechthoekige of ronde filterplaten, voorzien van een filterdoek. Twee van deze holle platen tegen elkaar vormen een filterkamer. Elke plaat heeft veelal twee holle kanten. De platen aan de uiteinden van de pers hebben elk maar een holle kant. Het totaal aantal kamers in een kamerfilterpers is dan ook het aantal platen minus een.
De filterpers werkt niet continu zoals een zeefbandfilter, maar in batch. Eerst perst een hydraulische cilinder de platen naar elkaar toe[2] onder een hoge druk tot wel 500 bar. Deze druk is nodig om te voorkomen dat er vloeistof weglekt tussen twee platen. Vervolgens worden de kamers (de ruimtes tussen de platen) geladen met de suspensie. Deze suspensie wordt onder toenemende druk (veelal tot 15 bar) van de voedingspomp ingedikt.
De vaste delen worden in de kamers gehouden door het filterdoek. De vloeistof die door het doek gaat wordt ook wel filtraat genoemd. Dit filtraat wordt via speciale kanalen in de platen afgevoerd. Uiteindelijk worden de platen weer gescheiden, waarna de filterkoek verwijderd kan worden uit de kamers. Dan herhaalt de cyclus zich[3].
Het watergehalte in de filterkoek die overblijft hangt af van de fysische en chemische eigenschappen van de suspensie en van de druk waarmee de suspensie in de filterpers gepompt wordt. Een watergehalte van minder dan 65% in de filterkoek is in veel gevallen haalbaar[4].
Constructie van filterpersen
Filterpersen als apparaat voor koekfiltratie hebben een filterpakket gevormd door filterplaten in een rek dat is geplaatst tussen een vast deksel en een beweegbaar deksel. Tussen de afzonderlijke filterplaten bevinden zich filtermedia (weefsel of membraan). De vaste kap is via verbindings- en trekstangen met de brug verbonden. Een hydraulische drukinrichting, die is geïntegreerd in de brug en werkt op het beweegbare deksel, drukt op het filterpakket. De contactdrukken liggen tussen 250 en 600 bar. Deze hoge drukken zorgen voor de dichtheid van het filterpakket. De leidingen voor de toevoerleidingen van de ophanging zijn geïntegreerd in de vaste kap. De doorgang voor de ophanging in het filterpakket bevindt zich in het midden van de filterplaten.
Filtratieproces van filterpersen
In de filterkamers wordt de suspensie met behulp van een pomp met 10-20 bar tegen de filterdoeken gepompt. De vloeistof passeert het filtermedium en verlaat de pers via afvoerkanalen. De vaste delen van de suspensie blijven op het filtermedium en vormen de filterkoek. Na voltooiing van de filtratiecyclus wordt de pers geopend en de cake verwijderd. Voor zover de pers dit niet automatisch doet (zelfreinigende kamerfilterpers), wordt de druk langzaam afgevoerd, wordt de filterpers geopend en wordt de cake met de hand van de filterdoeken verwijderd.[5]
Membraanfilterpersen hebben de speciale eigenschap dat de filterkoek ook mechanisch wordt uitgeperst. Voor dit doel heeft elke filterkamer ten minste één beweegbaar membraan. Dit membraan wordt geplaatst nadat de instroom van de suspensie is gestopt door middel van perslucht of water onder druk in de richting van de filterkoek in beweging en drukt deze bovendien naar buiten.
Soorten filterpersen
Kamerfilterpers
De kamerfilterpers is een betrekkelijk eenvoudige maar krachtige uitvoeringsvorm van een filterpers, die worden gebruikt in de vaste stof-vloeistofscheiding van suspensies. Het maakt niet uit of het gaat om het product te filteren om een suspensie van de mijnbouw, voedingsmiddelen, chemische en farmaceutische industrie of afvalwater proces. Vanwege hun eenvoud en flexibiliteit, de kamerfilterpers in vele toepassingen is een kosteneffectieve en betrouwbare machine voor vast-vloeistofscheiding bij een Nachpresseinrichtung met overeenkomstige membraan plaatsystemen ter verhoging van het droge stofgehalte van de filterkoek is niet vereist. Daarbij kamerfilterpersen bereikt de respectieve invloed op de mate van droogte van de filterkoek, afhankelijk van de suspensie en ontwateringseigenschappen van maximaal vastestofgehalte in de filterkoek 30 tot ongeveer 50 procent (volgens vering soms ook hoger).
Membraanfilterpers
Membraanfilterpersen maken door het gebruik van membraantechnologie in de filterplaten hebben een grote invloed op de mate van droogte van de vaste en bereiken van de gebruikelijke filtratie werkwijze, de laagste restvochtigheid in de filterkoek (met uitzondering van hoge temperatuur filterpers). Een flexibel, ondoorlaatbaar membraan, dat is bevestigd aan het draaglichaam, in casu comprimeren cake in de kamer nadat het laden is voltooid. Deze enorme prestatie maakt het membraan filter drukt u op een van de systemen meest gebruikte en leg ze op een conventionele ontwatering proces onovertroffen voor vaste stoffen basis. kan worden bereikt door het opnieuw indrukken van membraanschotels significante verschillen in drogestofgehalte in de filterkoek, afhankelijk van de mate van uitdroging. Het bereik van haalbare drogestofgehalten (gewicht percentage van vaste stoffen in de filterkoek) verklaart strekt zich uit van 30 tot meer dan 80 procent.
Geautomatiseerde filterpers
Geautomatiseerde filterpersen conventioneel filterpersen, die echter met betrekking tot de mate van automatisering en bijgevolg continubedrijf volgens de bijzondere eisen van een snelle cyclustijd rechttrekken. In termen van de architectuur, het werkingsprincipe en procestechniek Dankzij de diverse automatiseringsprojecten opties (voor & nbsp; .. B automatische filter plaat verschuiving, filterkoek vrijlating hulp, filterdoek wasinrichting) ook een zeer snelle taart vrijlating en een verminderde cyclustijd kan worden gerealiseerd. Het resultaat is een snelle filterpers, die zorgt voor verhoogde productie per oppervlakte-eenheid van het filter.
Toepassingen
Filterpersen zijn veelzijdig. De grootte van de te scheiden vaste stoffen varieert van het μm-bereik (bijvoorbeeld enzymen) tot het mm-bereik (bijvoorbeeld rioolslib). De filteroppervlakken variëren van minder dan 1 m² voor kleine laboratoriumprocessen tot meer dan 1000 m² voor grote persen. Ze worden gebruikt in de voedingsindustrie, de chemische stof. de keramische of farmaceutische industrie. Ze zijn ook te vinden in de metallurgie en mijnbouw.
Huidige ontwikkeling
In de toekomst zullen de eisen van de markt voor de moderne filtratie-industrie steeds fijner en groter worden in de scheiding, en in het bijzonder met het doel van materiaalrecycling, energiebesparing en groene technologie. Om te voldoen aan de toenemende vraag naar een hogere graad van ontwatering uit moeilijk filterbaar materiaal, zijn superhoge drukfilters vereist. Daarom zal de trend in het verhogen van de druk voor de automatische filterpers zich in de toekomst blijven ontwikkelen.
De conventionele filterpersmechanismen gebruiken gewoonlijk mechanische compressie en lucht naar de-liquoring; de efficiëntie van het produceren van cake met laag vochtgehalte is echter beperkt. Een alternatieve methode is geïntroduceerd door het gebruik van stoom in plaats van lucht voor het ontwateren van de koek. Stoomontwateringstechniek kan een competitieve methode zijn, omdat het product van een vochtarme cake wordt aangeboden.[6]
Hete filterpers
De hete filterpers combineert de standaardprocesstappen van een membraanfilterpers (filtratie, filterkoekwassen en persen), met de extra functie van een thermische filterkoekdroging (TCD). Dientengevolge worden alle processtappen uitgevoerd in één installatie, de hete filterpers. Het ontwateren en drogen van de resulterende filterkoek wordt aldus uitgevoerd zonder een stroomafwaarts droogproces. In de basisversie komt het technische ontwerp overeen met een conventionele filterpers met een platenpakket membraanplaten. Filtreren, wassen en persen worden zoals gebruikelijk uitgevoerd. In tegenstelling tot de conventionele methode bestaat het systeem uit membraanfilterplaten en warmtewisselaarplaten, die afwisselend in een filterpers worden geïnstalleerd. Voor thermisch drogen wordt hete stoom en / of olie aangebracht op de werkruimte achter het membraan en de filterkoek wordt dienovereenkomstig thermisch gedroogd. Het voordeel van dit proces is dat een hoog drogestofgehalte (DM-gehalte) van meer dan 90% wordt bereikt.
Bronnen, noten en/of referenties
|