Weld nut
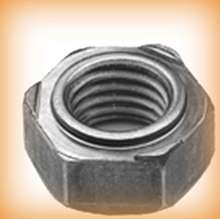
A weld nut is a special type of nut specifically designed to be welded to another object. There are various types for different applications.
History
The year was 1919 and World War 1 had officially ended after four years of intense fighting. President Woodrow Wilson established the Wartime Welding Committee of the Emergency Fleet Corporation under the leadership of Dr. Comfort Avery Adams. Adams, along with his 20-member committee; founded the American Welding Society as a nonprofit organization dedicated to the advancement of welding and allied processes. The Welding Journal was born and has been continually published since 1922.
This led to several advances and widespread use of welding in industrial processes. Stud Welding was first developed in the 1930’s at the New York Navy Yard. This new technique of rapidly joining a metal stud to a base via a projection and electrical current proved vital to the success of the war effort. Stud Welding, along with the advent of the automatic welding machines created the demand for similar “flash welded” products.
The first known patent for mass produced Weld Nuts (formerly known as welding nuts) were submitted by Leo Demboski and John Kay on April 20, 1936. The pair filed U.S. Patent no. 2,073,467 as assignors to The Ohio Nut & Bolt Company in Berea, Ohio. There invention utilized the same principal of projection stud welding in that a boss or projection would be rapidly heated and fused onto a supporting material. Thus, the first projection weld nuts were designed, submitted and mass produced.
Types
- Round base nuts
These nuts have a long threaded cylinder with a large circular base to make welding easy. They also sometimes have projections (known as weld nibs or bosses) to keep the nut from warping while welding with a high current.[1]
- Slab base nuts
These are very similar to the round base nuts, but with an obround, or slab shaped, base. These are used in channels, tubes, or other tight quarters.[1]
- Tab base nuts
Tab base nuts are designed for spot welding on flat workpieces. They have a locating boss around the threads to locate it in a pilot hole.[1]
- Hex & square nuts
These nuts are very similar to standard square or hex nuts, but have a locating boss and welding projections. The bosses also keep weld spatter out of the threads.[2]
- Retainer weld nuts
Retainer weld nuts, also known as bridge weld nuts, have a floating nut retained inside a retainer to compensate for inconsistencies. The retainer is welded to the workpiece while the nut is allowed to float.[2]
- Tube end nuts
Tube end nuts are sized to fit into the end of standard sized tubing, thus creating a threaded tube from standard stock.[2]
- Twin Piloted Nuts
Dual hole or twin piloted nuts are designed for use where there is a need for tapped holes close together.[3]
Material
The vast majority of weld nuts are manufactured in low carbon steel or stainless steel. This is due to the methods currently available to spot weld or projection weld the hardware to joining material. Aftermarket products such as zinc plating are sometimes used to coat low carbon weld nuts giving it the rust resistant properties of stainless steel at a substantial cost savings.
References
Notes
Bibliography
- McMaster-Carr catalog (114th ed.), McMaster-Carr .
- Buckeye Fasteners catalog (2018 ed.), Buckeye Fasteners Company .