Lithium–silicon battery
Lithium–silicon battery is a name used for a subclass of lithium-ion battery technology that employs a silicon-based anode and lithium ions as the charge carriers.[1] Silicon has a much larger specific capacity (3600 mAh/g) than graphite (372 mAh/g).[2] Silicon's large volume change (approximately 400% based on crystallographic densities) when lithium is inserted is one of the main obstacles along with high reactivity in the charged state to commercializing this type of anode.[3] Commercial battery anodes may have small amounts of silicon, boosting their performance slightly. The amounts are closely held trade secrets, limited as of 2018 to at most 10% of the anode.
History
The first laboratory experiments with lithium-silicon materials took place in the early to mid 1970s.[4]
Silicon-graphite composite electrodes
Silicon carbon composite anodes were first reported in 2002 by Yoshio [5] Studies of these composite materials has shown that the capacities are a weighted average of the two end members (graphite and silicon). On cycling electronic isolation of the silicon particles tends to occur with the capacity falling off to the capacity of the graphite component. This effect has been tempered using alternative synthetic methodologies or morphologies that can be created to help maintain contact with the current collector. This has been identified in studies involving grown silicon nanowires that are chemical bonded to the metal current collector by alloy formation. Sample production of batteries using a silicon NW -graphite composite electrode were produced by Amprius in 2014.[6] The same company claims to have sold several hundred thousand of these batteries as of 2014.[7] In 2016, Stanford University researchers presented a method of encapsulating silicon microparticles in a graphene shell, which confines fractured particles and also acts as a stable solid electrolyte interphase layer. These microparticles reached an energy density of 3,300 mAh/g.[8]
In 2015, Tesla founder Elon Musk claimed that silicon in Model S batteries increased the car’s range by 6%.[9]
As of 2018, products by startups Sila Nanotechnologies, Global Graphene Group, Enovix, Enevate, and others were undergoing tests by the battery manufacturers, car companies, and consumer-electronics companies. Sila clients include BMW and Amperex Technology, battery supplier to companies including Apple and Samsung. BMW plans to incorporate Sila technology by 2023 and increase battery-pack capacity by 10-15%.[10]
Specific capacity
Anode material | Specific capacity (mAh/g) | Volume change |
---|---|---|
Li | 3862 | - |
LiC 6 |
372 | 10% |
Li 13Sn 5 |
990 | 252% |
Li 9Al 4 |
2235 | 604% |
Li 15Si 4 |
3600 | 320% |
A crystalline silicon anode has a theoretical specific capacity of 3600 mAh/g, approximately ten times that of anodes such as graphite (372 mAh/g).[3] Each silicon atom can bind up to 3.75 lithium atoms in its fully lithiated state (Li
3.75Si), compared to one lithium atom per 6 carbon atoms for the fully lithiated graphite (LiC
6).[13]
[14]
Silicon swelling
The lattice distance between silicon atoms multiplies as it accommodates lithium ions (lithiation), reaching 320% of the original volume.[3] The expansion causes large anisotropic stresses to occur within the electrode material, fracturing and crumbling the silicon material and detachment from the current collector.[15] Prototypical lithium-silicon batteries lose most of their capacity in as little as 10 charge-discharge cycles.[4][16] A solution to the capacity and stability issues posed by the significant volume expansion upon lithiation is critical to the success of silicon anodes.
Because the volume expansion and contraction properties of nanoparticles differ greatly from the bulk, silicon nanostructures have been investigated as a potential solution. While they have a higher percentage of surface atoms than bulk silicon particles, the increased reactivity may be controlled by encasement, coatings, or other methods that limit surface—electrolyte contact. One method identified by researchers has used silicon nanowires on a conductive substrate for an anode, and found that the nanowire morphology creates direct current pathways to help increase power density and decreases disruption from volume change.[17] However, the large volume change of the nanowires can still pose a fading problem.
Other studies examined the potential of silicon nanoparticles. Anodes that use silicon nanoparticles may overcome the price and scale barriers of nanowire batteries, while offering more mechanical stability over cycling compared to other silicon electrodes.[18] Typically, these anodes add carbon as a conductive additive and a binder for increased mechanical stability. However, this geometry does not fully solve the issue of large volume expansion upon lithiation, exposing the battery to increased risk of capacity loss from inaccessible nanoparticles after cycle-induced cracking and stress.
Another nanoparticle approach is to use a conducting polymers matrix as both the binder and the polymer electrolyte for nanoparticle batteries. One study examined a three-dimensional conducting polymer and hydrogel network to encase and allow for ionic transport to the electrochemically active silicon nanoparticles.[19] The framework resulted in a marked improvement in electrode stability, with over 90% capacity retention after 5,000 cycles. Other methods to accomplish similar outcomes include utilizing slurry coating techniques, which are inline with presently used electrode creation methodologies.[20]
Charged Silicon Reactivity
Besides the well recognized problems associated with large volume expansion, for example cracking the SEI layer, a second well recognized issues involves the reactivity of the charged materials. Since charged silicon is a lithium silicide, its salt-like structure is built from a combination of silicon (-4) Zintl anions and lithium cations. These silicide anions are highly reduced and display high reactivity with the electrolyte components that is charge compensated locally by reduction of the solvents.[21][22] Recent work by Han, et al., has identified an in-situ coating synthesis method that eliminates the redox activity of the surface and limits the reactions that can take place with the solvents. Although it does not effect the issues associated with volume expansion, it has been seen with Mg cation based coatings to increase the cycle life and capacity significantly [23] in a manner similar to the film forming additive fluoroethylene carbonate (FEC).[24]
Solid electrolyte interphase layer
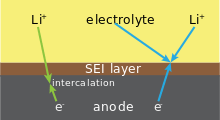
Another issue is the destabilization of the solid electrolyte interphase (SEI) layer consisting of decomposed electrolyte material.[25]
The SEI layer normally forms an ion conductive layer that is solvated by the electrolyte, which prevents further growth. However, due to the swelling of the silicon, the SEI layer cracks and become porous.[26] Thus, it can thicken. A thick SEI layer results in a higher cell resistance, which decreases cell efficiency.[27][28]
The SEI layer on silicon is composed of reduced electrolyte and lithium.[27] At the operating voltage of the battery, the electrolyte is unstable and decomposes.[25] The consumption of lithium in the formation of the SEI layer further decreases the battery capacity.[28] Limiting growth of the SEI layer is therefore critical for commercial lithium-silicon batteries.
References
- Nazri, Gholam-Abbas; Pistoia, Gianfranco, eds. (2004). Lithium Batteries - Science and Technology. Kluwer Academic Publishers. p. 259. ISBN 978-1-4020-7628-2.
- Zuo, Xiuxia; Zhu, Jin; Muller-Buschbaum, Peter; Cheng, Ya Chin (2017). "Silicon based lithium-ion battery anodes: A chronicle perspective review". Nano Energy. 31 (1): 113–143. doi:10.1016/j.nanoen.2016.11.013.
- Mukhopadhyay, Amartya; Sheldon, Brian W. (2014). "Deformation and stress in electrode materials for Li-ion batteries". Progress in Materials Science. 63: 58–116. doi:10.1016/j.pmatsci.2014.02.001.
- Lai, S (1976). "Solid Lithium Silicon Electrodes". Journal of the Electrochemical Society. 123 (8): 1196–1197. Bibcode:1976JElS..123.1196L. doi:10.1149/1.2133033.
- Yoshio, Masaki; Wang, Hongyu; Fukudu, Kenji; Umeno, Tatsuo; Dimov, Nickolay; Ogumi, Zempachi (2002). "Carbon-Coated Silicon as a Lithium-Ion Battery Anode Materials". Journal of the Electrochemical Society. 149 (12): A1598. Bibcode:2002JES.....115029L. doi:10.1149/1.1518988. ISSN 0013-4651.
- St. John, Jeff (2014-01-06). "Amprius Gets $30M Boost for Silicon-Based Lithium-Ion Batteries". Greentechmedia. Retrieved 2015-07-21.
- Bullis, Kevin (10 January 2014). "Startup Gets $30 Million to Bring High-Energy Silicon Batteries to Market". MIT Technology Review.
- Li, Yuzhang; Yan, Kai; Lee, Hyun-Wook; Lu, Zhenda; Liu, Nian; Cui, Yi (2016). "Growth of conformal graphene cages on micrometre-sized silicon particles as stable battery anodes". Nature Energy. 1 (2): 15029. Bibcode:2016NatEn...115029L. doi:10.1038/nenergy.2015.29. ISSN 2058-7546.
- Rathi, Akshat (2019-04-08). "How we get to the next big battery breakthrough". Quartz. Retrieved 2019-08-18.
- Wesoff, Eric (2019-04-17). "Daimler Leads $170M Investment in Sila Nano's Next-Generation Battery Tech". Green Tech Media. Retrieved 2019-08-18.
- Besenhard, J.; Daniel, C., eds. (2011). Handbook of Battery Materials. Wiley-VCH.
- Nazri, Gholam-Abbas; Pistoia, Gianfranco, eds. (2004). Lithium Batteries - Science and Technology. Kluwer Academic Publishers. p. 117. ISBN 978-1-4020-7628-2.
- Tarascon, J.M.; Armand, M. (2001). "Issues and challenges facing rechargeable lithium batteries". Nature. 414 (6861): 359–67. Bibcode:2001Natur.414..359T. doi:10.1038/35104644. PMID 11713543.
- Galvez-Aranda, Diego E.; Ponce, C. (2017). "Molecular dynamics simulations of the first charge of a Li-ion—Si-anode nanobattery". J Mol Model. 23 (120): 120. doi:10.1007/s00894-017-3283-2. OSTI 1430651. PMID 28303437.
- Berla, Lucas A.; Lee, Seok Woo; Ryu, Ill; Cui, Yi; Nix, William D. (2014). "Robustness of amorphous silicon during the initial lithiation/delithiation cycle". Journal of Power Sources. 258: 253–259. Bibcode:2014JPS...258..253B. doi:10.1016/j.jpowsour.2014.02.032.
- Jung, H (2003). "Amorphous silicon anode for lithium-ion rechargeable batteries". Journal of Power Sources. 115 (2): 346–351. Bibcode:2003JPS...115..346J. doi:10.1016/S0378-7753(02)00707-3.
- Chan, Candace K.; Peng, Hailin; Liu, Gao; McIlwrath, Kevin; Zhang, Xiao Feng; Huggins, Robert A.; Cui, Yi (Jan 2008). "High-performance lithium battery anodes using silicon nanowires". Nature Nanotechnology. 3 (1): 31–35. Bibcode:2008NatNa...3...31C. doi:10.1038/nnano.2007.411. PMID 18654447.
- Ge, Mingyuan; Rong, Jiepeng; Fang, Xin; Zhang, Anyi; Lu, Yunhao; Zhou, Chongwu (2013-02-06). "Scalable preparation of porous silicon nanoparticles and their application for lithium-ion battery anodes". Nano Research. 6 (3): 174–181. doi:10.1007/s12274-013-0293-y. ISSN 1998-0124.
- Wu, Hui; Yu, Guihua; Pan, Lijia; Liu, Nian; McDowell, Matthew T.; Bao, Zhenan; Cui, Yi (2013-06-04). "Stable Li-ion battery anodes by in-situ polymerization of conducting hydrogel to conformally coat silicon nanoparticles". Nature Communications. 4: 1943. Bibcode:2013NatCo...4.1943W. doi:10.1038/ncomms2941. ISSN 2041-1723. PMID 23733138.
- Higgins, Thomas M.; Park, Sang-Hoon; King, Paul J.; Zhang, Chuanfang (John); McEvoy, Niall; Berner, Nina C.; Daly, Dermot; Shmeliov, Aleksey; Khan, Umar (2016-03-22). "A Commercial Conducting Polymer as Both Binder and Conductive Additive for Silicon Nanoparticle-Based Lithium-Ion Battery Negative Electrodes". ACS Nano. 10 (3): 3702–3713. doi:10.1021/acsnano.6b00218. hdl:2262/77389. ISSN 1936-0851. PMID 26937766.
- Han, Binghong; Piernas Munoz, Maria; Dogan, Fulya; Kubal, Joseph; Trask, Stephen T.; Vaughey, John; Key, Baris (2019-07-05). "Probing the Reaction between PVDF and LiPAA vs Li7Si3: Investigation of Binder Stability for Si Anodes". Journal of the Electrochemical Society. 166 (12): A2396. doi:10.1149/2.0241912jes.
- Key, Baris; Bhattacharyya, Rangeet; Morcrette, M; Seznec, V; Tarascon, Jean Marie; Grey, Claire (2009-03-19). "Real-Time NMR Investigations of Structural Changes in Silicon Electrodes for Lithium-Ion Batteries". Journal of the American Chemical Society. 131 (26): 9239–49. doi:10.1021/ja8086278. PMID 19298062.
- Han, Binghong; Liao, Chen; Dogan, Fulya; Trask, Stephen; Lapidus, Saul; Vaughey, John; Key, Baris (2019-08-05). "Using Mixed Salt Electrolytes to Stabilize Silicon Anodes for Lithium-Ion Batteries via in Situ Formation of Li–M–Si Ternaries (M = Mg, Zn, Al, Ca)". ACS Applied Materials and Interfaces. 11 (33): 29780–29790. doi:10.1021/acsami.9b07270. PMID 31318201.
- Schroder, K; Alvarado, Judith; Yersak, T.A.; Li, J; Dudney, Nancy; Webb, L.J.; Meng, Y.S.; Stevenson, K.J. (2013-08-16). "The Effect of Fluoroethylene Carbonate as an Additive on the Solid Electrolyte Interphase (SEI)on Silicon Lithium-Ion Electrodes". Chemistry of Materials. 27: 5531–5542. doi:10.1021/acs.chemmater.5b01627.
- Chan, Candace K.; Ruffo, Riccardo; Hong, Seung Sae; Cui, Yi (2009). "Surface chemistry and morphology of the solid electrolyte interphase on silicon nanowire lithium-ion battery anodes". Journal of Power Sources. 189 (2): 1132–1140. Bibcode:2009JPS...189.1132C. doi:10.1016/j.jpowsour.2009.01.007. ISSN 0378-7753.
- Fong, Rosamaría (1990). "Studies of Lithium Intercalation into Carbons Using Nonaqueous Electrochemical Cells". Journal of the Electrochemical Society. 137 (7): 2009. doi:10.1149/1.2086855. ISSN 0013-4651.
- Ruffo, Riccardo; Hong, Seung Sae; Chan, Candace K.; Huggins, Robert A.; Cui, Yi (2009). "Impedance Analysis of Silicon Nanowire Lithium Ion Battery Anodes". The Journal of Physical Chemistry C. 113 (26): 11390–11398. CiteSeerX 10.1.1.465.1617. doi:10.1021/jp901594g. ISSN 1932-7447.
- Oumellal, Y.; Delpuech, N.; Mazouzi, D.; Dupré, N.; Gaubicher, J.; Moreau, P.; Soudan, P.; Lestriez, B.; Guyomard, D. (2011). "The failure mechanism of nano-sized Si-based negative electrodes for lithium ion batteries". Journal of Materials Chemistry. 21 (17): 6201. doi:10.1039/c1jm10213c. ISSN 0959-9428.