Back pressure
Back pressure (or backpressure) is a resistance or force opposing the desired flow of fluid through pipes, leading to friction loss and pressure drop. The term back pressure is a misnomer, as pressure is a scalar quantity, so it has a magnitude but no direction. The fluid is what is directed, tending to flow away from high-pressure regions and toward low-pressure regions. If the low-pressure space is more high-pressure than intended (e.g. due to obstructions or tight bends in an exhaust pipe) or the high-pressure space is more low-pressure than intended, this opposes the desired flow and reduces the discharge. Similarly, bending or other operations on a pipe (such as a stock car exhaust system with a particularly high number of twists and bends[1]) can reduce flow rate.
Explanation
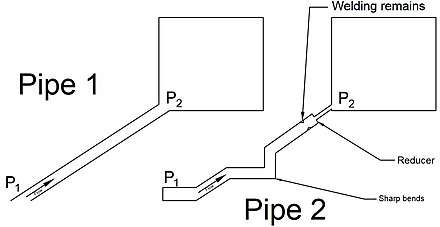
Fluid flows through a pipe because of the pressure difference between the two ends of a pipeline. The fluid will flow from the high-pressure end to the low-pressure end. Consider two systems as shown in the following figure. The flow in each case is caused by a pressure difference between P1 and P2. Pipe 2 has some obstructions (welding remains, a reducer, changes in area, sharp bends, etc.) which will create a pressure drop resulting in less discharge and a reduced rate of flow.
The loss of pressure or pressure drop was originally considered to be a result of a pressure exerted in the opposite direction by the obstructions, thereby canceling or reducing the applied pressure. This is the origin of the term backpressure.
A common example of backpressure is that caused by the exhaust system (consisting of the exhaust manifold, catalytic converter, muffler and connecting pipes) of an automotive four-stroke engine, which has a negative effect on engine efficiency, resulting in a decrease of power output that must be compensated by increasing fuel consumption.
In a piston-ported two-stroke engine, however, the situation is more complicated, due to the need to prevent unburned fuel/air mixture from passing right through the cylinders into the exhaust. During the exhaust phase of the cycle, backpressure is even more undesirable than in a four-stroke engine, as there is less time available for exhaust and the lack of pumping action from the piston to force the exhaust out of the cylinder. However, since the exhaust port necessarily remains open for a time after scavenging is completed, unburned mixture can follow the exhaust out of the cylinder, wasting fuel and increasing pollution. This can only be prevented if the pressure at the exhaust port is greater than that in the cylinder.
These conflicting requirements are reconciled by constructing the exhaust pipe with diverging and converging conical sections to create pressure wave reflections which travel back up the pipe and are presented at the exhaust port. The exhaust port opens while there is still significant pressure in the cylinder, which drives the initial outflow of exhaust. As the pressure wave from the pulse of exhaust gas travels down the pipe, it encounters a diverging conical section; this causes a wave of negative pressure to be reflected back up the pipe, which arrives at the exhaust port towards the end of the exhaust phase, when the cylinder pressure has fallen to a low level, and helps to draw the remaining exhaust gas out of the cylinder. Further along the exhaust pipe, the exhaust pressure wave encounters a converging conical section, and this reflects a positive pressure wave back up the pipe. This wave is timed to arrive at the exhaust port after scavenging is completed, thereby "plugging" the exhaust port to prevent spillage of fresh charge, and indeed may also push back into the cylinder any charge which has already spilled.
Since the timing of this process is determined mainly by exhaust system geometry, which is extremely difficult to make variable, correct timing and therefore optimum engine efficiency can typically only be achieved over a small part of the engine's range of operating speed.
For an extremely detailed description of these phenomena see Design and Simulation of Two-Stroke Engines (1996), by Prof. Gordon Blair of Queen's University Belfast, pub. SAE International, ISBN 978-1-56091-685-7.
Networking
In an analogy between physical fluids flowing through pipes and bits of information flowing through computer networks, "back pressure" is used to describe a feature of some networks such as Interlaken (networking) and others that use wormhole switching.
References
- Muffler at How Stuff Works