Manhès–David process
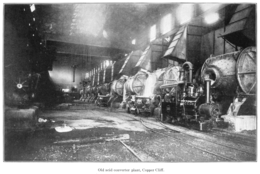
The Manhès–David process is a refining process of the copper mattes, invented in 1880 by the French industrialist Pierre Manhès and his engineer Paul David. Inspired by the Bessemer process, it consists of the use of a converter to oxidise with air the undesirable chemical elements (mainly iron and sulfur) contained in the matte, to transform it into copper.
The quantity of the elements to be oxidized, as well as the low heat produced by the chemical reactions, lead to drastics modifications of the converter. Manhès and David designed it as a horizontal cylinder, with nozzles aligned from one end to the other. A few years later, the Americans engineers William H. Peirce and Elias Anton Cappelen Smith lined it with basic refractory materials, much more durable than that used by the French inventors. While this improvement does not alter the principles of the process, it eases its widespread use, accelerating the switchover of copper production from Britain to the United States.
At the beginning of the 21st century, the Pierce-Smith converters refine 90% of the copper mattes and is used in 60% of the nickel extracted. This converter, like the addition of pure oxygen, the automation of the running, the treatment of smoke and the increasing size of the tools, ensured the durability of the Manhès–David process, even if modern tools have little relationship with their ancestors.
Converting in copper metallurgy
A mixture of copper and iron sulfides referred to as matte is treated in converters to oxidize iron in the first stage, and oxidize copper in the second stage. In the first stage oxygen enriched air is blown through the tuyeres to partially convert metal sulfides to oxides:
- FeS + O2 → FeO + SO2
- CuS + O2 → CuO + SO2
Since iron has greater affinity to oxygen, the produced copper oxide reacts with the remaining iron sulfide:
- CuO + FeS → CuS + FeO
The bulk of the copper oxide is turned back into the form of sulfide. In order to separate the obtained iron oxide, flux (mainly silica) is added into the converter. Silica reacts with iron oxide to produce a light slag phase, which is poured off through the hood when the converter is tilted around the rotation axis:
- 2 FeO + SiO2 → Fe2SiO4 (sometimes denoted as 2FeO•SiO2, fayalite)
After the first portion of slag is poured off the converter, a new portion of matte is added, and the converting operation is repeated many times until the converter is filled with the purified copper sulfide. The converter slag is usually recycled to the smelting stage due to the high content of copper in this by-product. Converter gas contains more than 10% of sulfur dioxide, which is usually captured for the production of sulfuric acid.
The second stage of converting is aimed at oxidizing the copper sulfide phase (purified in the first stage), and produces blister copper. The following reaction takes place in the converter:
- CuS + O2 → Cu + SO2
Copper content in the obtained blister copper is typically more than 95%. Blister copper is the final product of converting.
References
![]() |
Wikimedia Commons has media related to Manhès-David converters. |
- ↑ Coleman, Arthur Philemon (1913). The nickel industry; with special reference to the Sudbury region, Ontario. Ottawa Government Printing Bureau. pp. 143–144.